In the field of mechanical design and engineering, accurately calculating the number of coils of a spring is a crucial task. The number of coils of a spring directly affects its performance and application effect. Let’s discuss in detail how to calculate the number of coils of a spring.
Basic concept of spring coils
The number of coils of a spring is usually divided into effective coils, support coils and total coils.
The effective number of coils refers to the number of coils that participate in the deformation of the spring and provide elastic force.
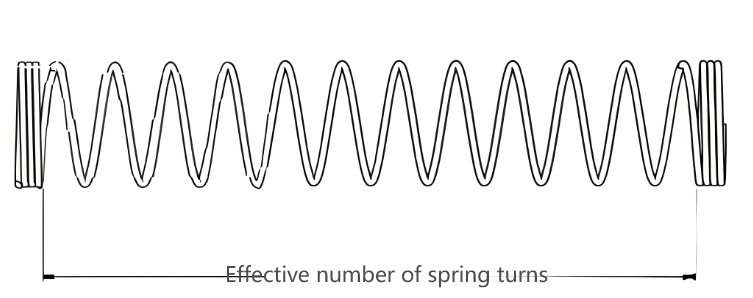
The support coils are additional coils set to make the spring uniformly stressed and supported when working, usually with 1-2 coils at each end.
The total number of coils is the sum of the effective number of coils and the support coils.
Methods for calculating the number of coils of a spring
Open-end grounded springs are different, and each end is considered to have about half of the inactive coils. This type of spring needs to be taken into account when designing and using it to accurately evaluate its performance and load-bearing capacity.
Springs with closed ends or closed and ground ends have an inactive coil at each end. This requires us to subtract the number of inactive coils at both ends when calculating the effective number of coils.
The number of spring turns is calculated from top to bottom. To do this, start at one end of the spring (where the wire is cut) and wind one turn around the wire, with each 360° turn being counted as a full turn. For example, if you wind 180°, it is 1/2 turn; if you wind 90°, it is 1/4 turn.
To make this clearer, let’s take a specific spring as an example. Suppose we have an open-ended spring, and we wind 8 full turns around the wire from the top, then the effective number of turns is 8 turns. For another example, if it is a closed and ground-end spring, and we also wind 8 full turns from the top, then the effective number of turns is 8 – 2 = 6 turns, because there is an inactive coil at each end.
What factors should be considered in practical applications to select the appropriate number of spring turns?
- Load requirements:
The size and range of loads to be borne. If the load is large and changes frequently, more turns may be required to provide sufficient elastic deformation and stability.
For example, in the automobile suspension system, in order to withstand the weight of the vehicle and various impact forces during driving, it is necessary to select a spring with a suitable number of turns according to the vehicle model and usage conditions to ensure smooth and comfortable driving. - Space limitation:
When the space size for installing the spring is limited, the number of turns must be selected on the premise of meeting the space requirements.
For example, the springs inside some precision instruments cannot have too many spring turns due to the compact overall structure of the instrument, so as not to occupy too much space. - Elastic coefficient requirements:
Different application scenarios have specific requirements for the elastic coefficient of the spring. By adjusting the number of turns, the elastic coefficient of the spring can be changed.
For example, in some shock absorbing devices, the spring needs to have a softer elasticity to absorb greater impact energy, which may require fewer turns. - Fatigue life:
Springs that are frequently used or in working condition for a long time need to consider their fatigue life. More turns may help disperse stress and extend the service life of the spring.
Like stamping die springs in industrial production, due to continuous reciprocating motion, sufficient turns are required to reduce the risk of fatigue damage. - Working environment:
Harsh working environments such as high temperature, corrosion, and humidity can affect the performance of springs. In these cases, the number of turns may need to be adjusted accordingly.
For example, for springs working in high temperature environments, the strength of the material will decrease, and the number of turns may need to be increased to ensure its load-bearing capacity. - Cost factors:
More turns usually mean higher material costs and manufacturing difficulties. On the premise of meeting performance requirements, the number of turns should be controlled as much as possible to reduce costs.
When choosing the appropriate number of spring turns, it is necessary to comprehensively consider factors such as load, space, elastic coefficient, fatigue life, working environment and cost to ensure that the spring can function reliably and effectively in actual applications.